摘 要:某气体公司发生一起充装二氧化碳的37Mn钢无缝钢瓶破裂爆炸事故.通过现场勘察与宏观分析、壁厚测量、化学成分分析、力学性能测试、金相检验、断口分析等方法,分析了钢瓶破裂爆炸的原因.结果表明:该钢瓶瓶体内壁发生了应力腐蚀开裂,在内部压力和搬运过程中的碰撞及振动作用下,钢瓶承压能力不足,最终导致钢瓶发生了物理破裂爆炸.最后,根据失效分析提出了相应的预防措施。
瓶装二氧化碳一般为高压液化气体,使用管理不当或者钢瓶存在质量缺陷都可能导致钢瓶失效甚至发生事故.充装高压二氧化碳的钢瓶一旦发生事故具有严重的破坏性,存在隐患的钢瓶就像炸弹一样,对人们的生命和财产安全存在着巨大威胁.失效分析是一门新兴的、发展中的学科,近些年来开始从军工普及到普通企业,在提高产品质量、技术开发和改进、产品修复及仲裁失效事故等方面具有很强的实际意义[1G2].广州某气体公司一个充装二氧化碳的37Mn钢无缝钢瓶在搬运过程发生破裂爆炸.由于37Mn钢二氧化碳钢瓶使用广泛,且其失效具有严重的破坏性,因此该起事故钢瓶的失效分析对同类事故的预防具有重要的实际价值.笔者通过现场勘察与宏观分析、壁厚测定、化学成分分析、力学性能测试、金相检验、断口分析等方法,研究了该二氧化碳钢瓶破裂爆炸的原因,并提出了预防措施。
1 现场勘查与宏观分析
对二氧化碳钢瓶的爆炸现场情况进行了勘查分析,并对钢瓶的开裂特征、内部裂纹和内部残留物等进行宏观 分 析,初 步 分 析 引 起 该 钢 瓶 破 裂 爆 炸 的原因.钢瓶钢印显示,失效钢瓶为1999年3月制造,工作 压 力 15.0 MPa,试 验 压 力 22.5 MPa,净 重49.4kg,容 积 41.4 L,公 称 壁 厚 5.0 mm,外 径219mm,钢瓶材料为37Mn钢.现场受钢瓶爆炸的影响较轻微,固定钢瓶的钢架一端有一定变形,钢架部分焊接接头发生撕裂,上方横梁有一个灯具损坏,其余灯具正常未受影响,地面、墙壁、房顶均未见明显损坏,见图1.
钢瓶宏观破裂特征如图2所示,最大裂口位于钢瓶瓶体的2/3高度位置(距离瓶底约800 mm),即图2中区域 A 和区域 B处.裂口沿着轴向扩展,向两侧撕裂,上端至瓶口处完全裂开,下端撕裂至瓶底位置.钢瓶内壁覆盖一层灰褐色残留物,下部有残留液态物,初步判断最大裂口区域 A 和区域 B处为起裂区.钢瓶破裂形状较规则,可初步判断钢瓶是由破裂导致物理爆炸.
在图2中区域 A 处,裂纹存在 Y 字形的分叉走向,对 Y 字形交叉开裂位置进行进一步宏观观察发现,该区域的断口粗糙,无明显塑性变形,沿着壁厚有明显的颜色差异,如图3所示.靠近内壁的部分呈深褐色,无金属光泽,有明显的放射状条纹,为陈旧断口.靠近外壁的部分呈青灰色,有金属光泽,为新鲜断口,与主断裂面约成45°.撕裂部位的断口平齐,呈青灰色,有金属光泽,与主断裂面约成45°.对区域 A 附近的剩余新鲜壁厚进行测量,发现钢瓶Y 字形开裂部位的最小剩余厚度约为1mm.对钢瓶内壁进行仔细观察,发现区域 A 和区域B附近有多条肉眼可见的未穿透裂纹,裂纹的长度方向和钢瓶的轴向基本平行,见图4.裂纹周边未见明显局部腐蚀坑,裂纹长度约为10mm.由以上观察结果初步判断:在破裂爆炸前,钢瓶内壁就存在未穿透裂纹,钢瓶承压能力不足;刚充装完成的钢瓶内部压力较大,在内部压力和搬运过程的振动作用下,最终钢瓶发生了物理破裂爆炸。
2 理化检验
2.1 壁厚测量
对钢瓶瓶体进行壁厚测量,结果显示钢瓶最小壁厚为5.0mm,满足设计壁厚(5.0mm)的要求,可见钢瓶未出现明显腐蚀减薄.
2.2 化学成分分析
对钢瓶瓶体材料进行火花直读光谱分析,结果显示钢 瓶 的 化 学 成 分 符 合 GB18248-2008
[3]对37Mn钢钢瓶材料的化学成分要求,见表1.
试验结束后,采用LEOG1450型扫描电镜对试样腐蚀形貌进行分析.
2.3 力学性能测试
从钢 瓶 瓶 体 截 取 纵 向 拉 伸 试 样,按 照 GB/T228.1-2010的要求进行拉伸试验,采取比例试样.
结果显示,试样的拉抗拉强度Rm 、规定非比例延伸强度Rp0.2和断后伸长率A 均满足 GB18248-2008对37Mn钢的技术要求,见表2.
2.4 金相检验
对钢瓶裂源区的材料进行金相检验,观察面为瓶体横截面.分析显示,钢瓶靠近外壁的显微组织为保持马氏体位相的回火索氏体+铁素体,未见带状组织,如图5所示.钢瓶壁厚中间部位组织为保持马氏体位相的回火索氏体+铁素体,未见明显的带状组织,如图6所示.钢瓶内壁附近显微组织也为保持马氏体位相的回火索氏体+铁素体,但靠近内壁有明显的带状组织(带状级别为 C2~C3)。
对裂源区区域 A 内壁上的一条穿透裂纹进行金相检验,观察面平行于内壁表面.检验结果显示,裂纹附近显微组织为保持马氏体位相的回火索氏体+ 铁 素 体,裂 纹 穿 晶 扩 展,局 部 存 在 分 支,如图8所示.对图8中裂纹尖端区域进行金相检验,观察面平行于内壁表面,可见显微组织也为保持马氏体位相的回火索氏体+铁素体,裂纹同样穿晶扩展。
2.5 断口分析
2.5.1 扫描电镜观察
在区域 B截取断口试样进行扫描电镜观察,发现钢瓶裂 源 区 断 口 沿 壁 厚 方 向 有 明 显 的 分 界,靠近内壁的绝大部分断口为陈旧断口,表面有一层覆盖物,掩盖了断裂特征,但仍然可见起源于内壁表面的放射状条纹;靠近外壁的小部分断口较干净,为新鲜断口,与主断裂面约成45°.对图10中的区域1和区域2进行局部形貌观察,见图11~12,发现断口表面受到氧化腐蚀,无法看清楚断口的原始显微形貌特征.区域2为区域1和区域3的交界处,对比可见区域1的腐蚀情况相对区域3的轻微一些,见图12.对区域3进行局部形貌观察,发现断口腐蚀严重,表面有一层腐蚀产物覆盖,也无法看清楚断口的原始显微形貌特征,见图13.
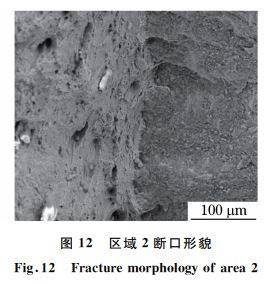
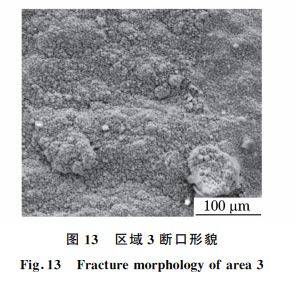
为进一步观察断口形貌,从区域 B附近截取一块断口,使用体积分数为1%的盐酸溶液及丙酮超声波清洗后再进行观察.低倍下可观察到陈旧断口处有明显的源于内壁的放射状条纹以及多条二次裂纹,可以清楚看到断口上有多条二次裂纹,见图15.
在图2中区域 A 附近截取一个带有未穿透裂纹的试样,研磨抛光后通过扫描电镜观察,可见裂纹具有一定分支,如图16所示.
2.5.2 能谱分析
从钢瓶内壁提取表面覆盖物进行能谱分析,并对钢瓶的陈旧断口和新鲜断口也进行了能谱分析,分析位置见图17.能谱分析结果显示:内壁粉末状覆盖物的主要元素成分有铁、氧、碳、硅、钙等,见图18;陈旧断口表面覆盖物的主要元素成分有铁、氧、碳、铁、硅、钙、氯、硫,如图19所示,其中,氯、硫等元素为有害元素;新鲜断口表面的主要元素有铁、锰,与陈旧断口和内壁覆盖物的化学成分存在明显差别,
较为轻微,钢瓶破口呈规则状态.一般来说,钢瓶化学爆炸的能量比物理爆炸的要大得多,发生化学爆炸时现场会受到较大影响,钢瓶也会受到较严重的
破坏,而且破坏基本是不规则的.通过钢瓶破裂断口的宏观观察可知,裂源区位于钢瓶2/3高度的部位为起裂源所在位置,裂源区附近内壁有陈旧断口
特征,钢瓶剩余壁厚约为1mm,同时裂源区附近有多条未穿透的纵向裂纹.综上可以判断,钢瓶是由于剩余壁厚承压能力不足,发生了物理破裂爆炸.
3.2 钢瓶应力腐蚀原因
分析金属构件发生应力腐蚀必须满足一定的拉应力、特定的腐蚀介质环境和材料的应力腐蚀敏感性3个要素.
(1)应力条件
应力腐蚀的出现一般仅需要较小的应力即可,充装二氧化碳产生的内部压力为钢瓶的应力腐蚀提供了应力条件.钢瓶充装二氧化碳后,钢瓶便承受了较大的拉应力,此应力条件可促进应力腐蚀的发生并以较快的速率进行.
(2)材料敏感性和介质环境条件
通过现场勘察和宏观分析发现,失效钢瓶内部存在水分.由能谱分析结果可知,陈旧断口表面覆盖物主要含有铁、氧、碳、硅、钙、氯、硫等元素,内壁粉末状覆盖物主要含有铁、氧、碳、硅、钙等元素.
该钢瓶为消防用二氧化碳气瓶,在充装二氧化碳后一般长期存放.在钢瓶内部,二氧化碳、水、氯离子等会形成复杂的介质环境,二氧化碳可以溶于水并与水发生反应生成碳酸,形成碳酸盐溶液环境或 CO2GHCO-3GCO2-3 的介质环境.相关文献表明,碳锰钢在 CO2GHCO-3GCO2-3 介质环境中可发生应力腐蚀[4].相关文献也表明,碳酸盐溶液是低碳钢和低合金钢的应力腐蚀敏感介质[5].由物相分析结果分知,陈旧断口表面和粉末状物质的主要成分均为 FeCO3,内 壁 粉 末 物 的 主 要 成 分 为 FeCO3 和SiO2,新鲜断口的主要成分为铁.由此可见,钢瓶内部发生了应力腐蚀,主要产物为 FeCO3.
3.3 应力腐蚀机理分析
在复杂 的 介 质 环 境 下,钢 瓶 内 部 初 期 会 产 生Fe3O4 钝化膜,直到表面钝化膜达到一定厚度并含有一 定 量 的 Fe2+ . 在 含 有 CO2GHCO-3GCO2-3 和Cl- 等的复杂介质环境下以及拉应力的作用下,钢瓶内壁具有微观孔洞等缺陷的部位由于应力集中的影响,表面的氧化膜被腐蚀而受到破坏.钢瓶内壁破坏的表面和未破坏的内壁表面分别形成阳极和阴极,内壁阳极处的金属成为离子而被溶解,并产生电流流向阴极.由于内部被破坏的阳极面积比阴极面积小得多,阳极的电流密度很大,并进一步腐蚀内壁上已破坏的表面,再加上钢瓶受压产生的拉应力作用,破坏处逐渐形成裂纹,裂纹逐渐扩展直至断裂.在钝化膜的破裂过程中,Fe2+ 与 HCO-3 ,CO2-3 反应主要生成 FeCO3,并成为最终的主要腐蚀产物[4].此应力腐蚀也可能由于一种反应而发展,即由阴极反应产生的氢离子 H+ 和 CO2GHCO-3GCO2-3 之间的相互作用,共同促进应力腐蚀的发展.另外,氯离子等杂质的存在也可能对应力腐蚀产生促进作用.
3.4 钢瓶使用管理因素分析
由检验结果可知,钢瓶内壁存在多条陈旧裂纹,且钢瓶没有进行定期检验,未及时发现钢瓶内部裂纹缺陷.从现场勘察和宏观分析可知,钢瓶外壁有明显的碰撞痕迹,钢瓶在运输过程中可能存在振动或碰撞.在振动和碰撞产生的冲击力作用下,钢瓶内部的裂纹逐步扩展,最终瞬间发生破裂爆炸.
4 预防措施
为预防钢瓶发生应力腐蚀开裂,可以通过采取预防措施控制应力腐蚀发生的条件.通过控制二氧化碳气体和钢瓶质量可以避免应力腐蚀介质和降低材料的腐蚀敏感性.加强气瓶的使用管理可以及时发现钢瓶的异常情况并及时处理,减少事故发生的可能性.
4.1 二氧化碳气体质量控制措施
二氧化碳气体质量控制包括生产环节和充装环节的质量控制,应尽量减少二氧化碳中水、氯离子、油等含量.钢瓶在干燥的气体环境中一般不会发生应力腐蚀开裂,但该钢瓶的应力腐蚀过程存在电化学腐蚀,因此应特别严格控制二氧化碳气体中的水含量,例如可以采取吸湿性液体吸收、用活性固体干燥剂吸收、用压缩或冷却方法冷凝等方法来减少二氧化碳气体中的水含量.
4.2 钢瓶制造质量控制措施
钢瓶制造材料、工艺等都可能导致钢瓶材质存在问题,不仅会影响钢瓶的力学性能,同时也会影响钢瓶的应力腐蚀敏感性.无缝钢瓶的制造过程可能会导致瓶体存在残余应力,并可能导致钢瓶发生应力腐蚀,可采取热处理措施,减小钢瓶瓶体的残余应力.在钢瓶制造完成后,应对钢瓶内部进行清洗和干燥,减少钢瓶内部水分和其他杂质的残留.在进行水压或气密性试验后,应采取内表面干燥处理,并予以密封.
4.3 钢瓶使用管理措施
钢瓶充装和使用单位应做好钢瓶的管理工作,并按照相关规定对钢瓶进行定期检验,及时发现钢瓶缺陷.应控制水压试验使用水中氯离子的含量,
减少氯离子在气瓶内的残留.在水压或气密性试验后,应对内表面进行干燥处理,并予以密封[6G7].钢瓶储存和运输过程应避免碰撞和跌落,并按要求做好定期检验工作.
5 结论及建议
综合分析认为,该失效的钢瓶具备应力腐蚀开裂的特征和条件,瓶体内壁发生了应力腐蚀开裂.在内部压力和搬运过程的碰撞及振动作用下,钢瓶承压能力不足,最终导致钢瓶发生了物理破裂爆炸.
建议加强对二氧化碳钢瓶的生产、储存运输、充装和使用的监管,确保各环节的规范管理,同时我们也要经常做失效分析的试验,减少类似事故的发生。
标签: